世界最大煤制油裝置
——鄂爾多斯煤直接液化裝置
工程投資額:245億元
工程期限:1998年——2020年
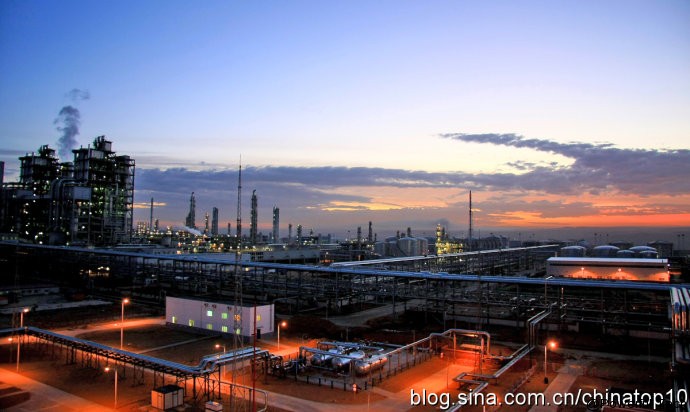
中國神華鄂爾多斯煤制油公司的龐大廠區(qū),這是目前世界最大的煤炭直接液化裝置。
煤炭和石油都是重要的天然能源,但石油對世界經(jīng)濟的影響力要遠高于煤炭。因1973年中東戰(zhàn)爭、1979年兩伊戰(zhàn)爭和1990年海灣戰(zhàn)爭,引起的三次世界石油危機,都曾使世界經(jīng)濟嚴重衰退。近年來隨著國際油價一路飛漲,石油能源安全問題,再次牽動著世界經(jīng)濟的神經(jīng)。
我國是個煤炭資源豐富,而石油資源較為貧乏的國家,已探明煤炭資源儲量約13000億噸,居世界第三位,2008年煤炭產(chǎn)量27.16億噸,居世界第一位。我國已探明石油儲量約155億桶(2007年),居世界第14位。2008年中國原油產(chǎn)量1.89億噸,居世界第五位。隨著經(jīng)濟高速增長,自2003年起,我國已成為僅次于美國的世界第二大石油消費國,石油進口量逐年增加,2008年進口原油1.789億噸,居世界第二位。隨著石油進口依存度迅速提高,我國能源安全,已成為不可回避的現(xiàn)實問題,尋找石油替代能源擺上了國家議事日程。而以煤炭為原料,通過化學加工過程生產(chǎn)石油產(chǎn)品(簡稱煤制油),對于優(yōu)化我國能源結(jié)構(gòu),保持國民經(jīng)濟可持續(xù)發(fā)展,具有重要的戰(zhàn)略意義。
2008年12月30日14時46分,目前世界最大的煤制油項目——神華集團鄂爾多斯煤直接液化示范工程,第一條百萬噸級生產(chǎn)線投煤試車;于12月31日7時,打通全部生產(chǎn)流程,順利實現(xiàn)油渣成型,產(chǎn)出合格的柴油和石腦油。裝置連續(xù)運行303小時后按計劃停車。這標志著我國成為世界上唯一實現(xiàn)百萬噸級煤直接液化關(guān)鍵技術(shù)的國家。
.jpg)
神華鄂爾多斯百萬噸煤制油項目全景
□ 世界最大的煤炭直接液化裝置
神華集團是我國最大的煤炭企業(yè)、世界最大的煤炭供應商,前身為華能精煤公司。1985年1月,國家為加速電力發(fā)展,由國務院以煤代油專用資金辦公室等機構(gòu),出資設(shè)立華能精煤公司、華能國際電力開發(fā)公司等9家企業(yè)。1988年,國務院批準組建華能集團。1995年8月經(jīng)國務院批準,以華能精煤公司為基礎(chǔ),另行組建神華集團,主要負責國家四個跨世紀特大工程之一的“神華工程”(即西煤東運)。經(jīng)過十幾年發(fā)展,神華集團不斷壯大,截止2008年底,原煤產(chǎn)量2.82億噸,商品煤銷量3.2億噸,實現(xiàn)營業(yè)收入1406億元。集團擁有54個煤礦,員工總數(shù)15.9萬人,總資產(chǎn)4111億元,成為集煤礦、電力、鐵路、港口、煤化工等產(chǎn)業(yè)于一體的特大型能源企業(yè)。
早在1997年,神華集團就提出采用世界先進技術(shù),建設(shè)煤炭液化示范項目,作為替代能源的設(shè)想。該計劃得到國家的大力支持,1998年國務院將大約110億元的“煤代油基金”劃撥給神華集團。此后神華集團用3年時間,對煤樣進行煤液化試驗,對世界三大煤直接液化技術(shù)(美國HTI工藝、德國IGOR工藝和日本NEDOL工藝)進行對比;同時開展了技術(shù)調(diào)研,包括考察南非SASOL公司的煤間接液化技術(shù)。2000年左右,神華集團初步?jīng)Q定采用美國HTI煤直接液化工藝,并對工藝流程進行改進,建設(shè)小型試驗裝置。2001年3月,國務院批準神華集團的項目建議書,2002年8月批復可行性研究報告。2003年6月12日,負責煤液化工程實施的中國神華煤制油有限公司,在北京正式成立。2004年6月,具有神華自主知識產(chǎn)權(quán)的煤直接液化工藝技術(shù)通過評估和鑒定,2004年12月17日,神華集團上海煤制油研究中心,日耗煤6噸的直接液化實驗裝置試驗成功。至此,我國煤制油直接液化生產(chǎn)技術(shù)轉(zhuǎn)化,獲得初步成果。
2004年8月25日,神華集團煤直接液化項目,在內(nèi)蒙古自治區(qū)鄂爾多斯市,伊金霍洛旗烏蘭木倫鎮(zhèn),舉行了一期工程開工典禮。這里距離著名的成吉思汗陵不到20公里,是我國最大煤田——神府東勝煤田所在地,探明煤炭儲量2200多億噸,為煤制油提供了充足的資源保障。2005年4月18日,煤制油生產(chǎn)基地的建設(shè)工程正式拉開帷幕。
神華集團鄂爾多斯煤直接液化生產(chǎn)基地,總面積1.735平方公里,其中廠區(qū)占地69公頃,生產(chǎn)裝置占地11.6公頃,倉儲裝卸區(qū)占地10公頃,廠外工程占地94.5公頃。設(shè)計規(guī)模為年產(chǎn)500萬噸油品,分兩期建設(shè),一期工程總投資245.35億元,由3條主生產(chǎn)線(單條108萬噸)組成。每條生產(chǎn)線包括煤液化、煤制氫、溶劑加氫、加氫改質(zhì)和催化劑制備等14套主要生產(chǎn)裝置。一期工程建成后,每年消耗煤炭970萬噸,生產(chǎn)各種油品320萬噸,產(chǎn)品分布為:汽油50萬噸、柴油215萬噸、液化氣32萬噸、苯+混合二甲苯24萬噸。目前已經(jīng)建成的第一條生產(chǎn)線,由中石化十公司、中石化四公司、上海石化安檢等單位承建。年耗煤345萬噸,生產(chǎn)各種油品108萬噸。其中,柴油72萬噸、液化石油氣10.2萬噸、石腦油25萬噸、酚等其他產(chǎn)品0.8萬噸。
神華鄂爾多斯煤制油項目能否成功,直接關(guān)系到國家的能源戰(zhàn)略問題,因此國家領(lǐng)導人對此十分關(guān)心。2006年6月2日,溫家寶總理到鄂爾多斯視察工作,專程到神華煤直接液化工程現(xiàn)場進行調(diào)查研究。2007年11月17日,胡錦濤主席視察了神華煤制油工程建設(shè)現(xiàn)場,充分肯定了煤制油在國家能源發(fā)展中的戰(zhàn)略地位。2009年8月24日,習近平副主席在神華集團鄂爾多斯煤制油分公司考察時,詳細了解了煤直接液化項目的產(chǎn)品。目前神華第一條煤制油生產(chǎn)線已經(jīng)進入試生產(chǎn)階段,日產(chǎn)柴油2000噸,產(chǎn)品銷售勢頭良好。
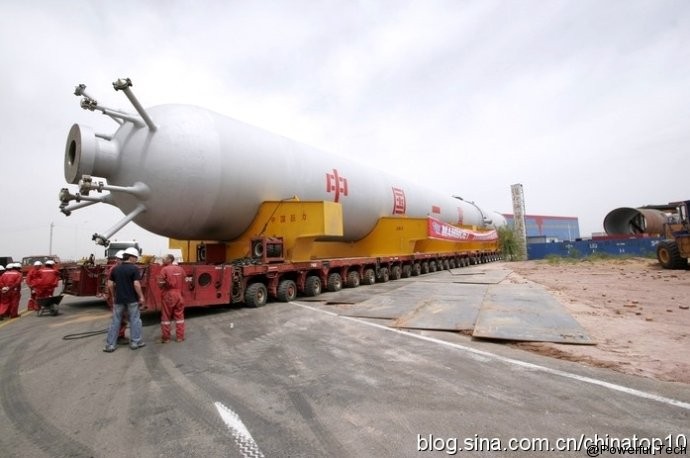
由中國一重集團為神華煤制油項目制造的世界最大煤液化加氫反應器,重達2044噸。
□ 龐大復雜的系統(tǒng)工程
為建造當今世界唯一的百萬噸級煤直接液化裝置,神華集團攻克了諸多技術(shù)難題。如神華集團自主開發(fā)的煤直接液化工藝,研制列入863計劃的新型納米級高效催化劑等。工程安裝世界最大的加氫穩(wěn)定(T-STAR)裝置,同時建設(shè)兩套每小時13.8萬立方米的煤制氫裝置,及世界首臺8800KW增安型無刷勵磁同步電機。項目建造的特大型型鋼混凝土框架高達82.7米,其土建施工難度堪稱石化行業(yè)之最。鋼結(jié)構(gòu)安裝近4萬噸,各類管道安裝近600公里,解決了最厚達88mm的347H不銹鋼厚壁管道焊接與熱處理技術(shù)。安裝各類設(shè)備2000多臺,其中超過200噸的設(shè)備多達25件,包括重達490噸的解壓蒸餾器、2個重達487噸的氣化爐,還有一個反應器重達1225噸,僅設(shè)備吊裝費用就高達數(shù)億元。
由中國一重為該項目制造的兩臺煤液化加氫穩(wěn)定(T-STAR)裝置,反應器直徑5.486米,高度57.776米,單臺重達2044噸,規(guī)格居世界之最。設(shè)備壁厚334mm,內(nèi)容積688立方米;由13個筒節(jié)、2個封頭及裙筒、裙座組成,部件在一重制造完成后,運至工地進行現(xiàn)場焊接。僅一道焊縫就需要連續(xù)焊接7-8天,熔填焊絲1噸。2006年6月17日,沈陽MAMMOET重型設(shè)備運輸安裝公司,采用3000噸級MSG-80型環(huán)軌式起重機,成功將巨型反應器吊裝到位,創(chuàng)造了同類設(shè)備吊裝的世界記錄。
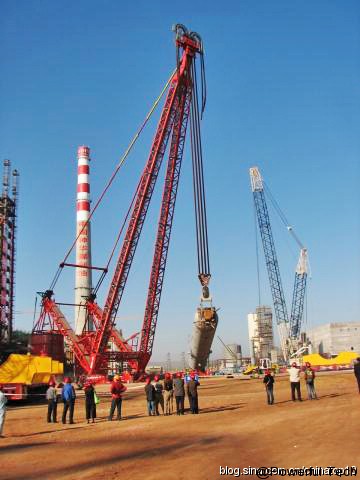
瑪姆特使用3000噸級環(huán)軌氏起重機,吊起世界最大的加氫反應器(2044噸),僅此項吊裝費用就達近億元。
□ 煤液化技術(shù)工藝流程
煤和石油都是碳氫化合物,所含化學元素基本相同。它們在化學組成上的差別是,煤的碳含量高,氫含量比石油低,氧含量比石油高。典型煙煤的氫碳比為0.8左右,而原油的氫碳比為1.76左右,汽柴油的氫碳比為2左右。煤液化就是根據(jù)大分子學說,讓煤在高溫高壓條件下裂解,通過化學反應提高煤炭的氫碳原子比,降低氧碳原子比,轉(zhuǎn)化成液態(tài)油(烷烴)和氣態(tài)烴。根據(jù)初步測算,每3.4-3.5噸煤可生產(chǎn)1噸油品,如果每桶原油價格保持在40美元以上,工業(yè)化煤制油生產(chǎn)就可以實現(xiàn)盈利。
目前世界煤液化技術(shù)主要包括直接液化、間接液化和煤焦油加工三種途徑。早在1927年德國就建成了世界第一座煤炭直接液化工廠,1934年德國又建成世界第一座煤炭間接液化工廠。這些工廠在二戰(zhàn)后,大都停產(chǎn)或轉(zhuǎn)產(chǎn)。煤炭直接液化的優(yōu)點是油品產(chǎn)率高,缺點是對煤種比較挑剔,化學反應條件苛刻。間接液化的優(yōu)點是煤種適應范圍廣,反應條件要求比直接液化低,缺點是油品產(chǎn)率低。兩種工藝在技術(shù)上具有互補性。
煤直接液化的流程是:將洗精煤送入備煤裝置,粉碎成特別小的粒度,摻上供氫溶劑制成煤漿。然后在煤液化裝置的高溫高壓環(huán)境(溫度420-480℃,壓力17-70MPa)以及催化劑作用下,煤的大分子結(jié)構(gòu)橋鍵斷裂,裂解成分子量相對較小的自由基碎片。由于自由基碎片是不帶電子的基團,自身不穩(wěn)定,需要送至加氫穩(wěn)定裝置,再通過一系列加氫化學反應及催化劑作用,使自由基碎片在高壓氫氣中加氫穩(wěn)定,脫除煤中氧、氮、硫等雜原子,再經(jīng)過加氫改質(zhì)裝置進一步提高油品質(zhì)量,生成柴油、汽油、石腦油等液態(tài)油(烷烴)和液化石油氣(LPG)等產(chǎn)物。反應過程中產(chǎn)生的含硫氣體、油渣、酸性水、含硫污水可經(jīng)過回收裝置處理后再循環(huán)利用。
煤間接液化的流程是:用煤炭干餾得到焦炭,焦炭在高溫下與氧氣和水蒸氣反應,制得的粗煤氣經(jīng)變換、脫硫、脫碳制成潔凈的一氧化碳與氫氣混合物。合成氣在催化劑作用下,經(jīng)F-T(費托)合成反應,生成烴類產(chǎn)品和化學品,烴類經(jīng)進一步加工可以生產(chǎn)汽油、柴油和LPG等產(chǎn)品。間接液化根據(jù)加熱溫度,又分為高溫合成與低溫合成兩類工藝。
□ 博采眾長自主創(chuàng)新
國外煤直接液化技術(shù)主要有美國的SRC-1、SRC-2、EDS、H-COAL、HTI工藝,德國的IGOR工藝,英國的SCE工藝,日本的NEDOL工藝等。煤間接液化技術(shù)主要有南非SASOL公司的F-T合成技術(shù),荷蘭Shell公司的SMDS技術(shù),美國Mobil公司的MTG合成技術(shù)等。這些技術(shù)雖然經(jīng)過長期發(fā)展,但多數(shù)為小型實驗裝置,大規(guī)模工業(yè)化生產(chǎn)仍然缺乏經(jīng)驗。因此,神華集團選擇煤液化技術(shù),必然要經(jīng)過技術(shù)創(chuàng)新和工藝創(chuàng)新的過程。
神華集團在對各國工藝進行考察的基礎(chǔ)上,2000年左右,初步?jīng)Q定采用美國HTI工藝,理由是該工藝油收率高,可達到60%以上,膠體催化劑活性較好,同時設(shè)備易于大型化。因此在2000年8-9月,神華集團委托HTI公司在其3t/d中型連續(xù)試驗裝置上,進行了上灣煤(來自神華煤田)PDU液化試驗;并根據(jù)實驗結(jié)果編制煤液化單元的預可研工藝包,包括:備煤、催化劑制備、煤液化、在線加氫以及溶劑脫灰等工藝。
2000年底,國內(nèi)煉油專家在對HTI公司提交的預可研工藝包進行審查的時候,指出在線加氫存在諸多隱患,國內(nèi)煉油專家普遍認為:在神華一期工程中,穩(wěn)定加氫宜采用北京石油化工科學研究院的離線加氫技術(shù)。根據(jù)新的流程,HTI公司修改了工藝包,并于2001年11月-2002年1月,在HTI又進行了模擬工藝包設(shè)計流程的小型驗證試驗(30kg/d的CFU裝置)。在國家計委的主持下,2002年3月神華煤液化項目完成了可研審查工作,隨后報國務院審批,2002年8月國務院批準了神華集團建設(shè)煤液化示范廠的申請。
2002年9月,中石化工程建設(shè)公司完成了煤液化廠第一條生產(chǎn)線的總體設(shè)計。在審查完總體設(shè)計后,相關(guān)領(lǐng)導提出需改善煤液化廠的經(jīng)濟性和運行的平穩(wěn)性。此時煤科院模擬HTI工藝進行的試驗也很不順利,裝置運轉(zhuǎn)不起來。在此背景下,神華集團上下對HTI工藝有了更多的疑議和擔心,希望能對HTI工藝作進一步優(yōu)化。此時神華煤液化技術(shù)部的舒歌平,提出采用溶劑全加氫的技術(shù)方案(TOP-NEDOL流程),此方案克服了原工藝不能長周期穩(wěn)定運行的問題,而且提高了油品產(chǎn)出率,得到了專家認可。
催化劑也是煤液化項目中降低成本的關(guān)鍵技術(shù)之一。神華煤直接液化項目在最初設(shè)計時,所采用的是國外一家公司的催化劑,但這種催化劑原料研磨需要很多設(shè)備,且磨制成本偏高。為此煤液化課題組組長舒歌平,領(lǐng)導科研人員經(jīng)過1210次試驗,研制出新型高效合成催化劑。該產(chǎn)品具有成本低、活性高、添加量少等特點,油收率提高4-5%,每年可增加經(jīng)濟效益2.4億元。目前,神華煤直接液化工藝技術(shù)已經(jīng)獲得國家知識產(chǎn)權(quán)局的專利授權(quán),并在美國、德國、日本等13個國家申請了專利保護。
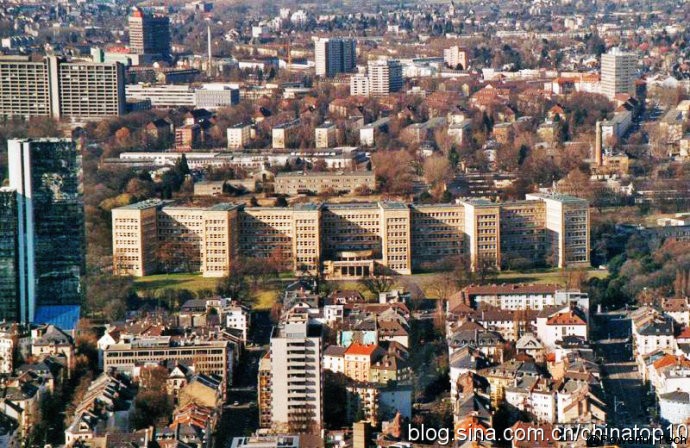
德國法蘭克福美因河畔的法本公司總部。法本化學康采恩(IG Farben)組建于1925年,由拜耳、赫希斯特、巴登苯胺公司(BASF公司前身)等6家德國大型化學公司合并而成,是當時世界最大的化工集團和德國最大的企業(yè)。1931年,法本向納粹黨和希特勒提供了大筆贈款幫助其競選,從中獲得了巨大的好處。到1943年,法本已壟斷了德國100%的合成橡膠、甲醇和潤滑油產(chǎn)量,以及98%的染料、95%的鎳和毒氣(包括全部齊克隆B)、90%的塑料、88%的鎂、80%的炸藥、70%的黑色火藥、46%的航空汽油和35%的硫酸。 法本在美國有規(guī)模龐大的子公司和工廠,并同美孚石油、杜邦化學、美鋁等托拉斯建立了密不可分的合作關(guān)系,1939年它從美孚進口了2000萬美元的航空汽油。美國參議院的一份報告中評價說:“沒有法本就不會有希特勒的戰(zhàn)爭”。法本還在奧斯維辛用活人進行拜耳開發(fā)的新型絕育藥物試驗。法本生產(chǎn)的齊克隆B通過拜耳交給一家叫Degesch(德國殺蟲劑公司)的經(jīng)銷商,然后出售給黨衛(wèi)軍,用于滅絕人類。二戰(zhàn)后法本被盟軍勒令拆分為拜耳(Bayer)、巴斯夫(BASF)、阿克發(fā)(Agfa)及赫希斯特等10家公司。這些都是當今世界赫赫有名的化工巨頭。
□ 世界煤制油產(chǎn)業(yè)發(fā)展概況
煤液化技術(shù)起源于德國,早在19世紀即已開始研究。德國是一個富煤貧油的國家,1913年,德國化學家弗里德里希·柏吉斯(F.Bergius),研究出煤炭在高溫高壓條件下加氫液化反應,生成燃料的煤炭直接液化技術(shù),并獲得專利。柏吉斯因此獲得1931年的諾貝爾化學獎。1923年,德國化學家費歇爾(F.Fischer)和托羅普希(H.Tropsch)試驗成功間接液化技術(shù)。1927年,德國法本(Farben)公司用柏吉斯法,在德國萊比錫附近的洛伊納(Leuna),建成世界第一座年產(chǎn)10萬噸的煤炭直接液化廠。1934年德國魯爾化學公司用費-托合成工藝,建成世界第一座年產(chǎn)7萬噸的煤炭間接液化廠。1935年,英國卜內(nèi)門化學工業(yè)公司,在比靈赫姆建起一座年產(chǎn)15萬噸的煤炭直接液化廠。此外,日本、法國、美國、加拿大等國,也先后建過一些實驗廠,世界年總產(chǎn)能達到約34萬噸。
日本同樣是石油資源貧乏的國家。1912年日本石油消耗量僅為4萬噸,到1932年已達到200萬噸。而同時期日本本土石油產(chǎn)量僅為42.7萬噸,臺灣產(chǎn)油3.5萬噸,不足需求量的五分之一。為了彌補石油產(chǎn)量不足,日本重點發(fā)展了所謂人造油,包括油頁巖制油、煤制油和松根汽油。1929年12月30日,撫順頁巖油廠落成,利用撫順煤礦的頁巖油層,用內(nèi)熱式干餾法提煉重油,日產(chǎn)4000噸,主要供應海軍艦艇使用。但這種方法生產(chǎn)的重油雜質(zhì)較高,艦艇燃油噴嘴經(jīng)常被堵塞,海軍非常氣憤。撫順頁巖油廠負責人長谷川清二因此引咎自殺。1931年日軍全面占領(lǐng)中國東北,這里豐富的煤炭資源,使日本開始關(guān)心煤炭液化技術(shù)。日本曾派考察團去德國和英國考察煤液化工廠,但英德將其視為軍事機密,導致日本人無功而返。撫順頁巖油工廠燃料課長阿部良之助等人,經(jīng)過長期實驗后,摸索出一套煤制油流程。即將煤和焦油1:1混合,以氧化鐵做催化劑,在100個大氣壓的氫氣下加熱到450攝氏度。其遵循的原理是,煤和石油相比,煤的氧多氫少,加高壓之后加氫,氧就已水的形式流出。但是試驗并不成功,阿部注意到應該先把煤這個大聚合體加以分解,于是把研究重點轉(zhuǎn)移到用以分解聚合體的催化劑上,最后找到了硫化亞鐵。其次,為了防止煤在粉碎過程中接觸空氣氧化,于是采取水中粉碎的方法,可是這樣做出來的是膠泥狀煤粉,最終采取在水中加入低溫焦油的方法提取煤粉。就這樣日本的煤炭液化技術(shù)取得了進展。
1937年日本的七年規(guī)劃,對于煤液化寄予了很大希望,計劃在1944年前,建成87個合成油裝置,總生產(chǎn)能力達到年產(chǎn)1300萬桶,滿足大約三分之一的需求,成為原油的重要補充。在這個計劃中,有10個是直接液化裝置,每個年產(chǎn)10萬噸,11個是間接液化的費托合成裝置,總產(chǎn)量50萬噸,其余的都是低溫焦化。1937年5月4日,日本海軍德山燃料廠決定采取阿部方式生產(chǎn)煤制油,由滿鐵出資1800萬日元建設(shè)新廠。1939年7月21日,工廠投產(chǎn),生產(chǎn)出日本第一批煤液化油,但產(chǎn)量少得可憐,只裝滿3個玻璃瓶。其中1瓶獻給了皇宮,另1瓶送給伊勢神宮,第3瓶送給阿部的母校,北海道輕臼小學。
此后受工業(yè)基礎(chǔ)限制,日本的煤制油始終不成氣候。最終,直接液化裝置在中國撫順和韓國各建了一個,只有撫順的投產(chǎn),到戰(zhàn)爭結(jié)束的時候總產(chǎn)量只有1000多噸。費托合成裝置在日本本土建立了三個,分別在1940、1942和1943年投產(chǎn)。在中國吉林和錦州還建成了兩套費托合成裝置,到戰(zhàn)爭結(jié)束時沒有完工。五個裝置的總設(shè)計生產(chǎn)能力是年產(chǎn)18萬噸,但實際上整個戰(zhàn)爭期間的總產(chǎn)量還不到6萬噸。最成功的是低溫焦化,建設(shè)了8個,實際年產(chǎn)量也只有幾萬噸,與規(guī)劃相去甚遠。太平洋戰(zhàn)爭后,美英對日本實施全面物資禁運。原油供應不足加速了日軍戰(zhàn)敗。為了省油,日軍飛行員幾乎沒有訓練的機會就被派到了戰(zhàn)場,損失可想而知。軍艦無油可燒,大部分被困在港里。于是,日本又發(fā)展了生物油技術(shù),各種各樣的油品都被用于軍事,豆油、菜籽油、松樹油等等只要是液體的就都成了好東西。曾經(jīng)有被擊沉的船只全部使用豆油的例子。這些都使得日本軍方的實力大受挫折,迅速崩潰。帝國海軍的象征——長期缺少油料的大和艦,在最后一次出海中被美軍擊沉。日本本土的合成油廠,大部分在1945年的大轟炸中被摧毀。

二戰(zhàn)中德軍燒木炭的坦克,石油資源匱乏加速了德國與日本的戰(zhàn)敗。
二戰(zhàn)期間,德國由于石油進口受到封鎖,在1936-1943年間重點發(fā)展煤制油技術(shù),先后建成9套煤炭間接液化裝置和18套煤炭直接液化裝置。1936年,德國的煤制油產(chǎn)量只有62萬噸,1939年達到220萬噸,1940年320萬噸,1941年390萬噸,1942年420萬噸,1943年達到戰(zhàn)時最高峰的560萬噸,1944年由于盟軍轟炸,產(chǎn)量降到約390萬噸,1945年降到110萬噸。在二戰(zhàn)期間,德國近三分之二的飛機燃料和50%的汽車及裝甲車用油,都由煤制油供應,產(chǎn)量遠遠高于天然石油。
二戰(zhàn)后,這些工廠在同盟國的干預下,全部停產(chǎn)或者轉(zhuǎn)產(chǎn),部分設(shè)備被瓜分。1952年,前蘇聯(lián)利用德國煤直接液化技術(shù)和設(shè)備,建成投產(chǎn)11座單臺產(chǎn)能4-5萬噸/年的裝置,運行7年后停產(chǎn)改作他用。由于中東石油的大規(guī)模開發(fā),石油價格下降,煤液化產(chǎn)品無法與石油競爭。這使得投資巨大、工藝流程復雜的煤制油技術(shù)產(chǎn)業(yè)化進程嘎然而止。隨后,西方發(fā)達國家對煤制油技術(shù)研究陷入低潮,甚至實驗裝置也都停止試驗。
當時,世界上只有南非重視煤炭液化技術(shù)。南非因種族隔離政策,長期遭到貿(mào)易禁運,而南非又是富煤貧油的國家,煤炭探明儲量587.5億噸,約占全非洲的三分之二,因此希望將其豐富的煤炭資源轉(zhuǎn)化成石油燃料。早在1927年,南非就開始探索煤液化技術(shù),由于南非的煤為高揮發(fā)高灰分的劣質(zhì)煤,所以當時選擇了間接液化工藝。
1955年南非薩索爾(SASOL)公司以煤為原料制造合成氣,通過對費-托合成工藝進行改進,建成第一座煤炭間接液化廠。至1958年,工廠的產(chǎn)能只達到設(shè)計能力的一半。在花費巨資改進后,至1960年才解決主要技術(shù)問題,達到每年30萬噸的設(shè)計產(chǎn)能。
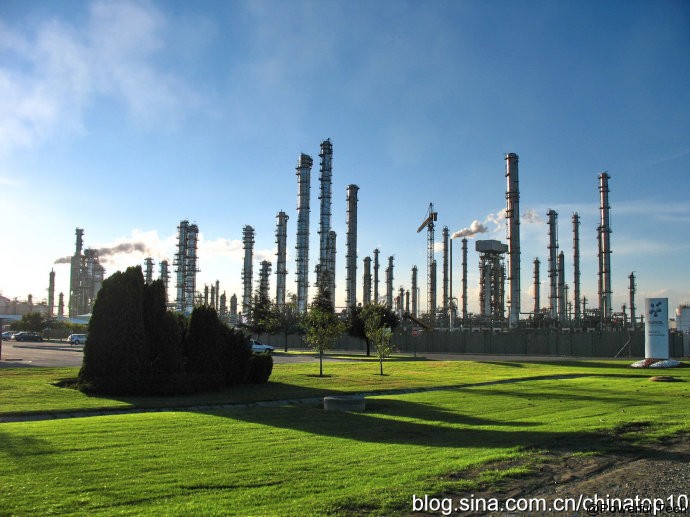
南非薩索爾(SASOL)煉油廠,是目前世界最大的煤制油生產(chǎn)商。
1973年后,由于在短短5年時間內(nèi)爆發(fā)了兩次中東戰(zhàn)爭,使得原油價格從每桶3.011美元提高到10.651美元。1978年的兩伊戰(zhàn)爭,使得兩伊石油產(chǎn)量從每天580萬桶驟降到100萬桶以下。油價開始暴漲,從每桶13美元猛增至1980年的34美元,從而引發(fā)了世界石油能源危機。在此背景下,煤炭液化技術(shù)又開始活躍起來。德國、美國、日本等工業(yè)發(fā)達國家,在原有基礎(chǔ)上相繼研究開發(fā)了第二代煤炭直接液化工藝。不少國家己完成了中間放大試驗,為建立大規(guī)模工業(yè)生產(chǎn)裝置打下了基礎(chǔ)。具有代表意義的有:德國日處理200噸煤炭的二段液化(IGOR)裝置,美國600噸/日的氫煤法H-coal裝置和日本鹿島150噸/日的NEDOL裝置。
1980年7月,南非薩索爾-2廠建成投產(chǎn),日處理煤炭4萬噸,年產(chǎn)汽油類燃料260萬噸。1982年薩索爾-3廠建成投產(chǎn),規(guī)模繼續(xù)擴大。這三座工廠年消耗原煤約4600萬噸,年產(chǎn)油品達768萬噸,包括汽油、柴油、蠟、氨等113種產(chǎn)品。該公司生產(chǎn)的汽油和柴油可滿足南非30%的消費量。
1992年,南非Mossgas公司采用SASOL公司開發(fā)的Synthol工藝,在南非莫塞爾灣建成天然氣制合成油(GTL)裝置。用海洋天然氣生產(chǎn)合成油品,年煉制能力為135萬噸,該廠是目前世界上最大的天然氣制合成油工廠。1993年殼牌石油在馬來西亞砂勞越州的Bintulu,建成年產(chǎn)50萬噸天然氣制合成油裝置。
80年代以后,由于經(jīng)歷兩次石油危機,世界經(jīng)濟嚴重衰退,對石油需求長期疲軟。盡管海灣戰(zhàn)爭曾使油價驟然回升,但戰(zhàn)爭結(jié)束后,油價又開始回落。1998年的油價跌到了1977年以來的最低水平。油價的起伏不定,使得美國的煤炭直接液化研究項目完成后,沒能如期進入工業(yè)化生產(chǎn)就被中斷。日本煤直接液化研究項目結(jié)束最晚,堅持到2000年,完成了日處理150噸煤炭的煤液化中試工廠項目。
從2003年起,世界對煤制油的熱情,因為油價的上升而重新燃起。目前,在全球范圍內(nèi),主要有十多個國家正在展開煤液化的商業(yè)化研究。主要國家有美國、中國、印度、德國、澳大利亞、印尼、日本、南非。隨著2008年爆發(fā)的全球金融危機,石油價格又從147美元的最高點回落到40美元左右,給煤制油產(chǎn)業(yè)化發(fā)展帶來了不確定性。目前在進行煤制油規(guī)模化生產(chǎn)嘗試的國家還有馬來西亞、巴西等國家,但沒有一個國家能超過百萬噸的生產(chǎn)能力。
通過分析這些國家的石油儲采比,可以發(fā)現(xiàn)對煤制油技術(shù)感興趣的國家,石油儲采比大都不到20年,遠遠低于國際平均水平(全球石油儲采比為40.5年)。同時,這些國家的石油進口占本國總消費量的比例一般都高于40%。
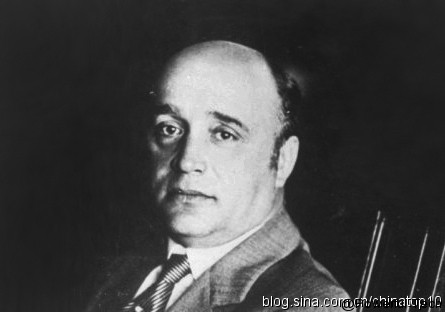
德國化學家弗里德里希·柏吉斯(Friedrich Bergius),他于1913年發(fā)明了煤直接液化工藝,并于1931年因其在化學高壓領(lǐng)域的貢獻,而獲得諾貝爾化學獎。
□ 中國煤制油發(fā)展歷史
我國曾是世界上較早有煤合成油工廠的國家之一。1923年,山西軍閥閻錫山計劃購買40架飛機成立航空兵團,同時提出要擁有500多輛汽車。因此山西當局為減少石油輸入量和發(fā)揮當?shù)孛禾康膬?yōu)勢,于1924年投資45萬元,從德國購置了一套煤炭間接液化裝置,在左云縣吳家窯建立了育才煉油廠。1925年,育才煉油廠略具雛形,開始以煤炭為原料采用低溫干餾法試煉油品,但因設(shè)備簡陋和技術(shù)不過關(guān)而未能成功。1926年,育才煉油廠又添置設(shè)施繼續(xù)試驗。同年,閻錫山參加直奉戰(zhàn)爭的軍隊駐扎該廠,工廠設(shè)施遭到損壞,無法繼續(xù)試驗。1930年中原大戰(zhàn)時期,閻錫山、馮玉祥倒蔣失敗,閻錫山逃往大連。至此,我國第一次煤制油試驗歷時5年多,未能取得成果。
1932年,閻錫山重回山西,因以前購買的機器陳舊、設(shè)備不全,他一面派人赴歐洲考察,一面添置新設(shè)備。1933年,山西育才煉油試驗廠改名為燃料研究所,并自造連續(xù)外熱式煉油爐一組,聘請德國工程師再次試驗煤制油。然而,試驗了一年也未成功。當時,德國的煤炭直接液化廠年產(chǎn)能已達10萬噸,英國也成功研制出了煤制汽油。山西于是又派人到英國和德國學習煉油技術(shù)。1935年,外派留學人員歸國,又從德國購回精制、煉油機器,以及內(nèi)熱式爐兩座、提煉爐一座、分餾釜一座。此后,燃料研究所開始對山西各地的不同炭種進行精制炭油試驗對比,每日干餾煤炭1噸,成功地生產(chǎn)出汽油、柴油、機器油、石蠟、瀝青等。當時的試驗結(jié)果顯示,噸煤所得制品最高紀錄是汽油76升、柴油61升、機器油16升、燃燒油42升、石蠟44千克、瀝青62千克、煤渣14千克。1937年,山西西北煉鋼廠利用燃料研究所,在煤制油實踐中總結(jié)出的技術(shù)參數(shù)和經(jīng)驗,配置了炭油蒸餾和汽油蒸餾設(shè)備,準備從煤焦化產(chǎn)品中提煉汽油,并計劃于當年10月1日正式投產(chǎn)。
然而,就在這個節(jié)骨眼上,“七七事變”爆發(fā)。日寇于1937年9月1日進犯晉北門戶天鎮(zhèn),11月8日侵占太原。燃料研究所和西北煉鋼廠從國外引進的裝置悉數(shù)被日軍掠奪,裝置被拆卸裝箱運到日本。我國第二次煤制油試驗就這樣被日寇所扼殺。1937年,日本出于侵略戰(zhàn)爭目的,在錦州石油六廠引進了德國煤制油裝置,項目于1943年投產(chǎn),1945年日本戰(zhàn)敗后企業(yè)停產(chǎn)。新中國成立后,我國重新恢復和擴建了錦州煤制油裝置,1959年規(guī)模最大時有70臺箱式反應器,年產(chǎn)油品4.7萬噸,1967年因大慶油田產(chǎn)油而停產(chǎn)。
1958年大躍進時期,山西再次開展煤制油試驗,全省共建成煤煉油廠34個。由于技術(shù)、成本和質(zhì)量都不過關(guān),這些煤煉油廠建成后都沒有生產(chǎn)出合格的汽油。后來這些廠陸續(xù)停產(chǎn)改建成縣級小氮肥廠。改革開放之后,山西煤制油試驗再次上馬。1981年,中科院山西煤化所開始進行煤制合成汽油的開發(fā)研究,并開發(fā)出兩段法煤制油試驗裝置。1989年5月至8月,山西省代縣化肥廠完成了兩段法煤制合成油的百噸級中試裝置,連續(xù)運行1600小時,共得汽油5.8噸,汽油收率為90-100克/立方米,油品辛烷值超過80。
1991年初,國家撥款600萬元,山西省自籌900萬元,利用晉城市第二化肥廠的廠區(qū)空地、公用設(shè)施和輔助生產(chǎn)裝置,建成規(guī)模為年產(chǎn)汽油2000噸、副產(chǎn)城市煤氣750萬立方米的工業(yè)化試驗裝置。1993年12月16日順利產(chǎn)出90號車用汽油,并通過了連續(xù)開車1500小時的考核。之后原化工部第二設(shè)計院開始進行年產(chǎn)5-10萬噸,煤制合成汽油大型裝置的方案設(shè)計工作。然而,由于當時國際石油價格很低,煤制油的成本高于進口石油,加上當時我國已開始大量進口石油,這套工業(yè)化試驗裝置也因經(jīng)費問題,在試驗成功后就不再開車了。
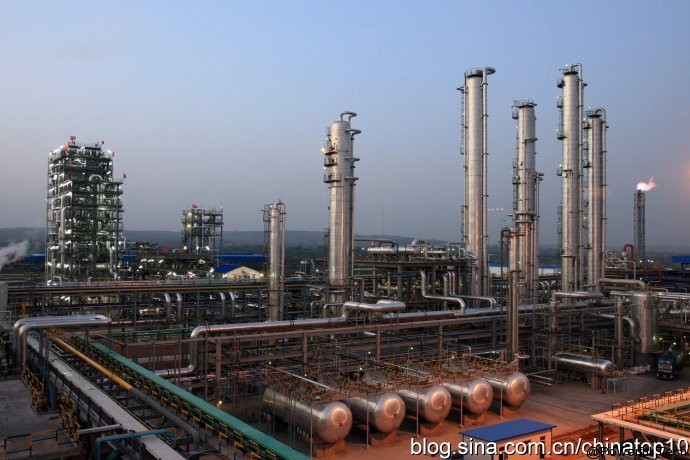
山西潞安礦業(yè)(集團)公司16萬噸年煤炭間接液化工業(yè)示范項目于2009年7月10日一次投料試車成功,產(chǎn)出合格油品。
□ 我國煤制油產(chǎn)業(yè)現(xiàn)狀
1997年以后,隨著我國石油需求快速增長,煤制油技術(shù)重新得到重視。目前我國在建和擬建煤制油裝置的公司,主要包括神華集團、兗礦集團、潞安礦業(yè)集團和內(nèi)蒙古伊泰集團。其中兗礦、潞安和伊泰采用煤間接液化技術(shù),神華集團采用煤炭直接液化工藝,并在寧夏寧東項目采用間接液化工藝。
早在1998年,山東兗州礦業(yè)集團已經(jīng)開始進行煤制油的技術(shù)儲備。當時,兗礦集團從南非薩索爾公司請回了其副總工程師孫啟文博士。孫的回國加快了煤間接液化技術(shù)研發(fā)。兗礦主要研究低溫鐵基漿態(tài)床技術(shù),和高溫鐵基固定流化床技術(shù)。2006年2月,兗礦集團在獲得國家發(fā)改委同意后,啟動了陜西榆林煤制油項目。計劃投資1000億元,分兩期建設(shè)1000萬噸煤間接液化項目。一期工程于4月21日奠基。準備投資134.5億元,在陜西榆林市榆橫煤化學工業(yè)區(qū)北區(qū),建設(shè)年產(chǎn)100萬噸的煤間接液化裝置。主要產(chǎn)品包括柴油78.08萬噸/年、石腦油25.84萬噸/年,液化石油氣5.648萬噸/年。但該項目受到國家政策轉(zhuǎn)向影響,仍處于審核溝通階段。
2006年2月22日,山西潞安礦業(yè)集團年產(chǎn)16萬噸煤間接液化示范裝置,在長治市屯留縣開工。該項目投資18.86億元人民幣,采用山西煤炭化學研究所自主研發(fā)的鈷基固定床費托合成技術(shù),2008年12月正式出油。按照規(guī)劃,潞安礦業(yè)集團準備在2015年前,建成2座年產(chǎn)260噸煤間接液化廠。
2006年5月11日,內(nèi)蒙古伊泰集團年產(chǎn)16萬噸煤間接液化示范裝置,在鄂爾多斯市準格爾旗大路煤化工園區(qū)正式開工。該項目投資21.76億元,設(shè)計生產(chǎn)規(guī)模為48萬噸/年,采用山西煤化所自主研發(fā)的鐵基漿態(tài)床費托合成技術(shù)。主要產(chǎn)品為柴油、石腦油及液化石油氣,2009年3月聯(lián)動試車、投料出油。2007年伊泰集團委托中國石油和化工規(guī)劃院編制了伊泰500萬噸煤制油項目規(guī)劃,擬投資661.4億元,分四期建成500萬噸產(chǎn)能。其中二期工程建設(shè)規(guī)模為350萬噸/年。
□ 三道禁令抑制投資過熱
2006年期間,隨著神華集團煤制油項目上馬,一大批煤制油項目聞風而動,導致煤制油“過熱”。在建和擬建的“煤制油”項目總產(chǎn)能達1600萬噸,計劃投入的資金額高達1200多億元。為此,國家發(fā)改委接連頒布了兩道禁令——“不批準年產(chǎn)規(guī)模在300萬噸以下的煤制油項目”,“在國家煤炭液化發(fā)展規(guī)劃編制完成前,暫停煤炭液化項目核準”。這兩道禁令使得諸多中小規(guī)模的項目陷入停滯,保留了神華、兗礦和潞安集團的煤制油項目,并列為煤制油樣板工程。
2008年9月4日,國家發(fā)改委再次發(fā)布煤制油的禁令。這份名為《關(guān)于加強煤制油項目管理有關(guān)問題的通知》(下稱《通知》)的文件明確指出,煤制油項目投資風險大,除神華集團鄂爾多斯煤直接液化項目、神華寧夏煤業(yè)集團的寧夏寧東煤間接液化項目需繼續(xù)按程序報批外,一律停止實施其他煤制油項目。
從我國煤制油的發(fā)展來看,盡管國家發(fā)改委連發(fā)三道禁令抑制投資過熱。但從能源布局出發(fā),近期煤制油、煤制烯烴、二甲醚、煤制天然氣和煤制乙二醇作為工業(yè)示范被列入石化振興規(guī)劃,體現(xiàn)了國家政策對穩(wěn)步發(fā)展煤化工的重視。同時,隨著國際油價重新回到70美元/桶之上,煤制油與煤化工進入了充分盈利區(qū)間,經(jīng)濟性得到改善。
預計到2020年,我國“煤制油”項目將形成年產(chǎn)5000萬噸油品的生產(chǎn)能力,加上屆時將有年產(chǎn)2000萬噸的生物質(zhì)油品投入使用,中國原油對外依賴程度有望從60%以上,降低到45%以下。
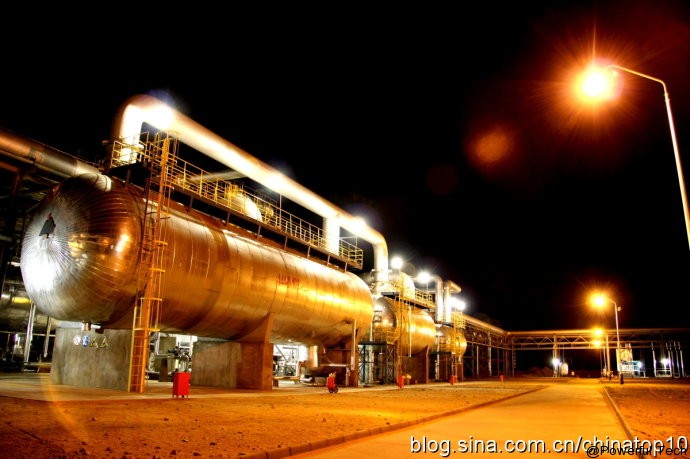
中國神華鄂爾多斯煤制油公司
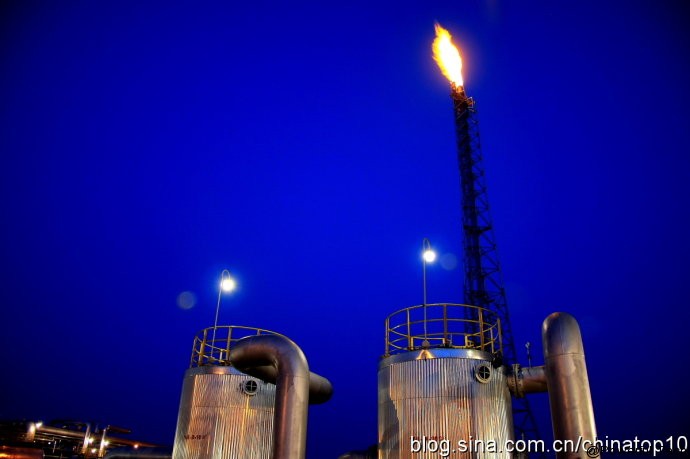
中國神華鄂爾多斯煤制油公司 燃燒著的火炬和低壓過濾罐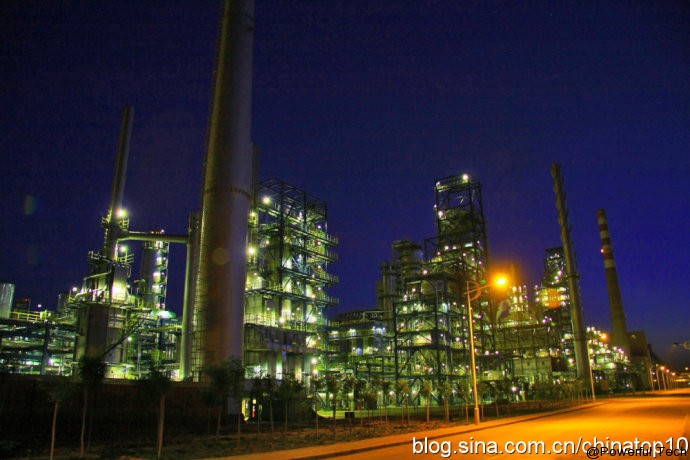
中國神華鄂爾多斯煤制油公司夜景。
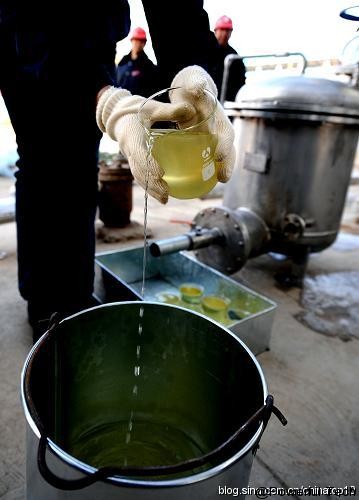
煤制油產(chǎn)品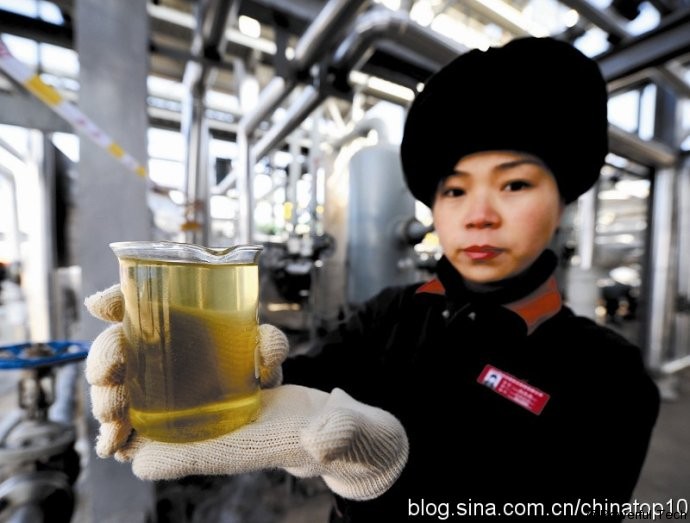
2009年12月22日,一名工作人員在山西潞安集團車間展示合成出來的原料油。
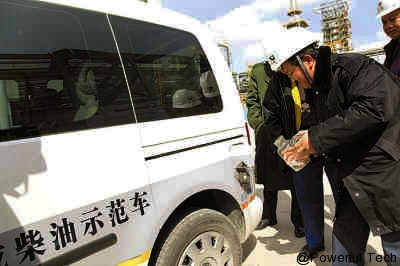
煤制油技術(shù)專家李永旺博士將柴油產(chǎn)品直接加入汽車
2007年11月17日,胡錦濤主席視察了神華集團煤直接液化建設(shè)工程現(xiàn)場,他充分肯定了煤制油在國家能源發(fā)展中的戰(zhàn)略地位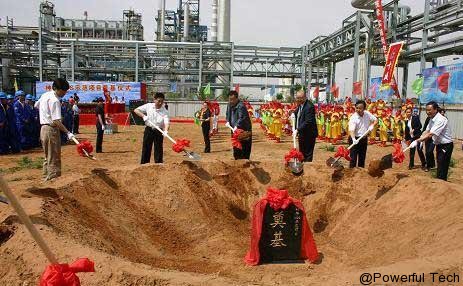
2010年6月1日,世界最大的二氧化碳捕集與封存(CCS)項目,在神華鄂爾多斯煤直接液化現(xiàn)場開工。煤制油會消耗大量水,釋放大量二氧化碳。隨著全球氣溫的不斷升高,二氧化碳的減排已刻不容緩。而在眾多減排方法中,碳捕集與封存技術(shù)成為目前最具可能性和現(xiàn)實意義的途徑,但目前僅有少數(shù)國家有小規(guī)模的工業(yè)應用。2009年,法國阿爾斯通(Alstom)公司在美國弗吉尼亞州登山家燃煤電廠(Mountaineer Plant)附近,投產(chǎn)了一套當時世界最大的碳捕獲設(shè)備,年捕捉二氧化碳約10萬公噸(占總排放量的1.5%)。捕獲的二氧化碳經(jīng)過液化后,以每小時5.5公斤的速度被運輸?shù)降叵?000米左右的蓄水層儲存。Mountaineer燃煤電廠建有世界最大的130萬千瓦超超臨界燃煤火力發(fā)電機組,該機組由阿爾斯通研制。西弗吉尼亞州有很多老舊的煤炭電廠,當?shù)卣M录夹g(shù)能夠保證這些工廠的就業(yè)情況。美國總統(tǒng)奧巴馬已劃撥了30億美元資金用于碳捕獲和儲存技術(shù)的發(fā)展。
神華集團CCS示范項目設(shè)計年捕集、封存二氧化碳10萬噸,概算投資約2.1億元,預計于2010年12月31日前建成投入運行。在示范項目的基礎(chǔ)上,未來將分兩步建成年收集與封存二氧化碳100萬噸、300萬噸的項目,其中100萬噸CCS項目正在做可行性研究工作,開工尚無明確時間表。在減排效果方面,年捕集封存100萬噸二氧化碳CCS項目建成后,可以回收神華煤制油工程全部生產(chǎn)過程中約三分之一的二氧化碳。此項目的主要工藝流程為:首先通過捕集、提純、壓縮、液化等收集到適合地下封存的二氧化碳,然后用低溫液體槽車將液體二氧化碳運送到距捕集地約17公里的封存區(qū)域,輸入三臺緩沖罐內(nèi)暫存,然后從罐底引出進入封存泵,升壓后注入地下1000米至3000米的巖層,并通過巖性較致密的蓋層實現(xiàn)密封。同時建設(shè)監(jiān)測井,用以監(jiān)測二氧化碳的擴散、運移狀態(tài)、有無泄露等。模擬運行表明,此裝置在1000年內(nèi)可以實現(xiàn)無泄露。
視頻:石油與戰(zhàn)爭
http://www.tudou.com/programs/view/uu94C_1Nito/